走査電子顕微鏡を使用して疲労破壊を観察し、破壊機構を分析した。同時に、脱炭した試験片に対して異なる温度でスピン曲げ疲労試験を実行し、脱炭ありとなしで試験鋼の疲労寿命を比較し、試験鋼の疲労性能に対する脱炭の影響を分析しました。結果は、加熱プロセスでは酸化と脱炭が同時に存在するため、両者の間の相互作用により、温度の上昇に伴って完全に脱炭された層の厚さが増加し、その後減少する傾向を示すことを示しています。完全脱炭層の厚さは750℃で最大値120μmに達し、850℃で完全脱炭層の厚さは最小値20μmに達し、試験鋼の疲労限界は約760MPaであり、試験鋼の疲労亀裂の原因は主に Al2O3 非金属介在物です。脱炭挙動は試験鋼の疲労寿命を大幅に短縮し、試験鋼の疲労性能に影響を与えます。脱炭層が厚くなるほど疲労寿命は低くなります。試験鋼の疲労性能に対する脱炭層の影響を軽減するには、試験鋼の最適熱処理温度を850℃に設定する必要があります。
歯車は自動車の重要な部品です高速で動作するため、歯面の噛み合い部分には高い強度と耐摩耗性が必要であり、歯元には材料の破損につながる亀裂を避けるために、一定の繰り返し荷重による良好な曲げ疲労性能が必要です。骨折。研究によると、脱炭は金属材料のスピン曲げ疲労性能に影響を与える重要な要素であり、スピン曲げ疲労性能は製品品質の重要な指標であるため、試験材料の脱炭挙動とスピン曲げ疲労性能を研究する必要があります。
この論文では,20CrMnTi歯車鋼の表面脱炭試験における熱処理炉,試験鋼の脱炭層深さの変化の法則を分析した。 QBWP-6000J簡易ビーム疲労試験機を使用して試験鋼の回転曲げ疲労試験を行い、試験鋼の疲労性能を決定すると同時に、実際の生産に向けて試験鋼の疲労性能に及ぼす脱炭の影響を分析し、改善を図ります。生産プロセスを監視し、製品の品質を向上させ、合理的な参照を提供します。試験鋼の疲労性能はスピン曲げ疲労試験機によって測定されます。
1. 試験材料と試験方法
ユニットの試験材料は、表 1 に示す主な化学組成の 20CrMnTi 歯車鋼を提供します。 脱炭試験: 試験材料を Ф8 mm × 12 mm の円筒形試験片に加工し、表面は汚れがなく光沢がある必要があります。熱処理炉で675℃、700℃、725℃、750℃、800℃、850℃、900℃、950℃、1,000℃に加熱し、試験片を1時間保持した後、室温まで空冷した。 4%の硝酸アルコール溶液浸食によるセッティング、研削、研磨による試験片の熱処理後、金属顕微鏡を使用して試験鋼の脱炭層を観察し、さまざまな温度での脱炭層の深さを測定します。スピン曲げ疲労試験:試験材料はスピン曲げ疲労試験片の2つのグループの処理の要件に従って、最初のグループは脱炭試験を実行せず、2番目のグループは異なる温度で脱炭試験を行います。スピン曲げ疲労試験機を使用して、スピン曲げ疲労試験用の2つのグループの試験鋼、2つのグループの試験鋼の疲労限界の決定、2つのグループの試験鋼の疲労寿命の比較、スキャンの使用電子顕微鏡で疲労破壊を観察し、試験片の破壊原因を分析し、試験鋼の疲労特性への脱炭の影響を調査します。
表1 供試鋼の化学組成(質量分率) wt%
脱炭に及ぼす加熱温度の影響
異なる加熱温度での脱炭組織の形態を図1に示します。図からわかるように、温度が675℃の場合、サンプル表面には脱炭層が現れません。温度が700℃に上昇すると、サンプル表面の脱炭層が現れ始め、薄いフェライト脱炭層が現れました。温度が725℃に上昇すると、サンプル表面の脱炭層の厚さが大幅に増加しました。 750℃の脱炭層の厚さは最大値に達し、この時点でフェライト粒子はより鮮明で粗大になります。温度が800℃に上昇すると、脱炭層の厚さは大幅に減少し始め、その厚さは750℃の半分に減少しました。温度が850℃まで上昇し続けたときの脱炭層の厚さを図1に示します。800℃では、完全な脱炭層の厚さは大幅に減少し始め、その厚さは半分で750℃まで低下します。温度が850℃以上まで上昇し続けると、試験鋼の完全脱炭層の厚さは減少し続け、半分の脱炭層の厚さは徐々に増加し始め、完全な脱炭層の形態がすべて消失し、半分の脱炭層の形態が徐々に明確になります。温度の上昇に伴って完全に脱炭された層の厚さが最初に増加し、次に減少したことがわかります。この現象の理由は、加熱プロセス中のサンプルが酸化と脱炭の挙動を同時に行うためです。酸化速度よりも脱炭速度が速いと脱炭現象が現れます。加熱の開始時、完全脱炭層の厚さは温度の上昇とともに徐々に増加し、完全脱炭層の厚さは最大値に達します。このとき、温度を上げ続けると、試験片の酸化速度はより速くなります。脱炭率が低下し、完全脱炭層の増加が阻害され、低下傾向となる。 675 ~ 950 ℃の範囲では、750 ℃での完全脱炭層の厚さの値が最も大きく、850 ℃での完全脱炭層の厚さの値が最も小さいことがわかります。したがって、試験鋼の加熱温度は850℃を推奨します。
図1 異なる加熱温度で1時間保持した試験鋼の脱炭層の組織形態
半脱炭層と比較して、完全脱炭層の厚さは材料特性により深刻な悪影響を及ぼし、強度、硬度、耐摩耗性、疲労限界の低下など、材料の機械的特性が大幅に低下します。 、などの亀裂の感受性も増加し、溶接の品質などに影響を与えます。したがって、完全脱炭層の厚さを制御することは、製品の性能を向上させる上で非常に重要です。図2は完全脱炭層の厚さの温度変化曲線を示しており、完全脱炭層の厚さの変化をより明確に示しています。図から、700℃では完全脱炭層の厚さはわずか約34μmであることがわかります。温度が725℃まで上昇すると、完全脱炭層の厚さは86μmに大幅に増加し、これは700℃での完全脱炭層の厚さの2倍以上になります。温度が750℃に上昇すると、完全脱炭層の厚さは温度が750℃に上昇すると、完全脱炭層の厚さは最大値120μmに達します。温度が上昇し続けると、完全に脱炭された層の厚さは急激に減少し始め、800℃では70μmとなり、850℃では最小値の約20μmになります。
図2 温度別の完全脱炭層の厚さ
スピンベンディングにおける疲労性能に及ぼす脱炭の影響
ばね鋼の疲労特性に及ぼす脱炭の影響を研究するために、2 つのグループのスピン曲げ疲労試験を実行しました。最初のグループは脱炭せずに直接疲労試験を行い、もう 1 つのグループは同じ応力で脱炭した後の疲労試験でした。レベル(810MPa)で脱炭処理を700~850℃で1時間保持した。試験片の最初のグループを表 2 に示します。これは、ばね鋼の疲労寿命です。
最初のグループの試験片の疲労寿命を表 2 に示します。表 2 からわかるように、脱炭なしでは、試験鋼は 810 MPa で 107 サイクルを受けただけであり、破壊は発生しませんでした。応力レベルが 830 MPa を超えると、一部の試験片が破損し始めました。応力レベルが 850 MPa を超えると、疲労試験片はすべて破壊されました。
表2 さまざまな応力レベルでの疲労寿命(脱炭なし)
疲労限界を決定するために、グループ法を使用して試験鋼の疲労限界を決定し、データの統計分析後の試験鋼の疲労限界は約 760 MPa です。さまざまな応力下での試験鋼の疲労寿命を特徴付けるために、図 3 に示すように SN 曲線をプロットします。図 3 からわかるように、疲労寿命が 7 の場合、異なる応力レベルは異なる疲労寿命に対応します。 、107 のサイクル数に対応します。これは、これらの条件下の試験片がその状態を通過していることを意味し、対応する応力値は疲労強度値、つまり 760 MPa として近似できます。 S-N 曲線は材料の疲労寿命を決定する上で重要な基準値であることがわかります。
図3 鋼製回転曲げ疲労試験実験のSN曲線
第 2 グループの試験片の疲労寿命を表 3 に示します。表 3 からわかるように、試験鋼をさまざまな温度で脱炭した後、サイクル数は明らかに減少し、107 回を超え、すべてのサイクル数が減少しました。疲労試験片が破壊され、疲労寿命が大幅に減少します。上記の脱炭層厚さと温度変化曲線を組み合わせると、750℃の脱炭層厚さが最も大きくなり、疲労寿命の最低値に相当します。 850℃の脱炭層の厚さは最も薄く、疲労寿命値が比較的高いことに対応します。脱炭挙動により材料の疲労性能が大幅に低下し、脱炭層が厚くなるほど疲労寿命が短くなることがわかります。
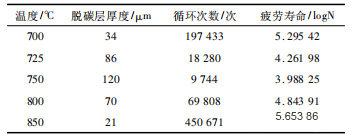
表3 各種脱炭温度における疲労寿命(560MPa)
図4に示すように、試験片の疲労破壊形態を走査型電子顕微鏡で観察しました。図4(a)は亀裂の発生源領域であり、図には明らかな疲労弧が見られ、疲労弧に従って発生源を見つけます。疲労亀裂の原因となる「魚の目」非金属介在物の亀裂の発生源であることがわかります。図4(b)は亀裂の伸長領域の形態を示しており、明らかな疲労縞が見られ、川状の分布であり、準解離破壊に属し、亀裂は拡大し、最終的に破壊に至ります。図 4(b) は亀裂の拡大領域の形態を示しています。明らかな疲労縞が川のような分布の形で見られます。これは準解離破壊に属し、亀裂の継続的な拡大に伴い、最終的に破壊に至ります。 。
疲労破壊解析
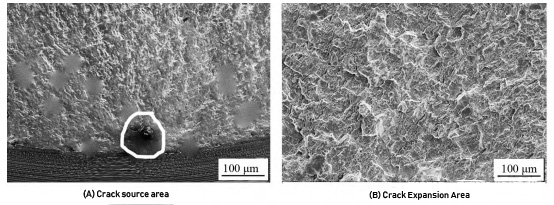
図4 試験鋼の疲労破面のSEM形態
図4の介在物の種類を判定するために、エネルギースペクトル組成分析を行った結果を図5に示します。非金属介在物は主にAl2O3介在物であることがわかり、介在物が存在していることがわかります。介在物の亀裂によって引き起こされる亀裂の主な原因となります。
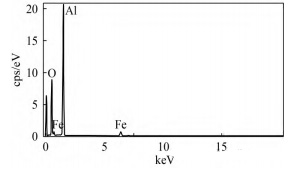
図5 非金属介在物のエネルギー分光分析
結論する
(1) 加熱温度を850℃とすることで脱炭層の厚みを最小限に抑え、疲労性能への影響を低減します。
(2) 試験鋼のスピン曲げの疲労限度は 760 MPa である。
( 3) 非金属介在物、主に Al2O3 混合物における試験鋼の亀裂。
(4) 脱炭は試験鋼の疲労寿命を著しく低下させます。脱炭層が厚くなるほど疲労寿命は低下します。
投稿日時: 2024 年 6 月 21 日